RobInspec
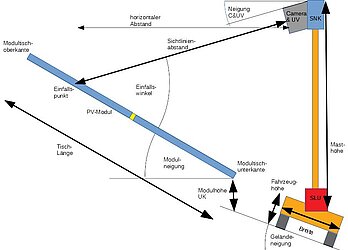
By the end of 2021, photovoltaic power plants installed in Germany boasted a nominal output of 59 GW, and this figure is trending upwards. However, for the energy transformation - a complete switch to CO2-neutral and sustainable energy supply, we need an order of magnitude of about 300 to 400 GW of installed PV capacity. The current plans of the German government envisage an additional 140 GW of power by 2030. Almost 30% of the installed PV capacity with photovoltaic open-space installations are a significant part of the overall market for photovoltaic systems in Germany, in addition to systems installed on roofs and facades.
This trend, in turn, brings up the question of the maintenance, service and inspection of increasing numbers of increasingly large solar parks. Compared to other energy producers, photovoltaic open-space systems require relatively little maintenance. However, they too need regular inspections to locate faults early on and minimize associated losses through their correction. Estimates for 2018 suggest that inspection and monitoring of PV plants in Germany alone could cost approximately USD 90 million per year and Europe-wide, the figure could reach USD 250 million.
These inspections are currently carried out by photovoltaic damage assessors. Inspecting a 50 MW plant requires four certified thermographers for a period of 14 days. In this project, the partners aim to develop an automated solution that significantly reduces the labour, time and costs involved in inspection. To this end, they plan to develop an autonomous mobile robot capable of fully automatic navigation of a solar park, conducting optical measurements as it goes. To achieve a suitable camera position for the measurements, a vertically extendable mast is planned to position the measuring equipment. Alongside the use of cameras in the visible and infrared spectrums for thermography, a new measurement method based on UV fluorescence (UVF) is also planned. This new method will enable, for the first time, analyses on the type and condition of the backside film by means of measurements taken from the front. Unlike thermography, which is ideally conducted under strong sun exposure, UVF measurement must be done at night. This makes a fully automated solution particularly advantageous for UVF, especially given that an autonomous robot with laser-based distance measurement does not rely on daylight. To facilitate automatic analysis with the various measurement methods, machine learning procedures are being developed in the project. Typical solar parks are located in uneven or inclined terrain. Therefore, the mast base will be equipped with a specially developed position compensation unit that ensures the system's position stability at all times. In addition to the use of cameras in the visible spectral range and infrared (IR) for thermography, a new measurement method using UV fluorescence is planned.